Preventing Air and Water Pollution
As a pharmaceutical company handling various chemical substances, the Daiichi Sankyo Group considers proper management of chemical substances as an important initiative and issue. To prevent air and water pollution, the group company plants outside of Japan, including Daiichi Sankyo Pharmaceutical (Shanghai), Daiichi Sankyo Europe (Germany), and Daiichi Sankyo Brasil Farmaceutica regularly monitor their emissions to ensure compliance with the laws and regulations of each country and region. In Japan, the Group has established voluntary control standards that are stricter than legal requirements and properly monitors the emissions at plants and research & development (R&D) centers in Group companies.
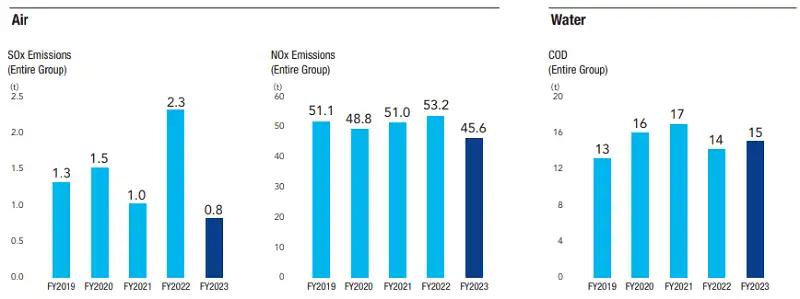
Data for each fiscal year is based on the company structure at that time
COD data is discharge wastewater into public waters
Preventing Soil and Groundwater Contamination and Countermeasures
The Group makes efforts to prevent soil and groundwater contamination at plants and research centers. In Japan, when an investigation is required based on the Soil Contamination Countermeasures Act and related prefectural ordinance, we conduct the appropriate investigation according to the laws and regulations on discussion with the governmental offices.
Furthermore, we also conduct investigations according to the laws and regulations even in the cases where mandatory regulations do not apply, such as the closing of offices and change of using purpose.
If contamination occurs, we report it to the related government offices and properly disclose information to members of the surrounding community, and take appropriate measures, such as prevention of diffusion and purification according to the extent of contamination. The offices that have already taken measures, such as purification, continue to monitor and report the result of analysis to governmental offices and community members.
Progress of Measures for Soil Purification
The site of former Yasugawa plant (Yasu City, Shiga)
|
We have been continuously monitoring the groundwater since we completed on-site environmental improvement work in 2006. As a result, contamination was found in part of the soil.
We are currently conducting a soil investigation in consultation with regulatory authorities to perform appropriate purification work. We also confirmed the presence of mercury used as a material for pesticides that exceeded environmental standards on the grounds of the former plant site in 1993.
Since then, we have installed a robust underground storage facility in adherence to regulatory guidance to manage the soil appropriately. Although there have been no reports of leakage or health issues to date, we decided to remove the storage facility in view of increasing safety and security in the region and in response to requests from the local community. We issued a press release announcing our decision in April 2020, and we are conducting removal work in consultation and coordination with all concerned parties.
During excavation, we take due care not to affect the surrounding environment through measures such as temporally setting up negative-pressure tents that cover the entire storage facility to prevent soil from scattering. |
Prevention of Noise, Vibration, and Offensive Odors
We conduct appropriate measures and continuous monitoring to comply with the laws and regulations related to noise, vibration, and offensive odor.
Appropriate Management and Emission and Transfer Control of Chemical Substances
We manage chemical substances that may adversely affect human health or the ecosystem based on the PRTR*1 system provided in the Act on Confirmation, etc. of Release Amounts of Specific Chemical Substances in the Environment and Promotion of Improvements to the Management Thereof.
There was no transport, import, export, or treatment of waste that was deemed hazardous or any transport of waste that was shipped internationally as described in the terms of the Basel Convention Annex I, II, III, and VIII.
*1Pollutant Release Transfer Register
Emission/Transfer Chemical Substances in FY2023 (Group in Japan)
(Unit: metric ton; mg-TEQ for dioxins)
Storage and Usage of PCB Contaminants
All PCB devices, etc. were properly disposed of by FY2021.
Evaluation of the Environmental Impact of Pharmaceutical Products
The Daiichi Sankyo Group conducts the necessary environmental impact assessments for its pharmaceuticals based on the guidelines of relevant countries and implements measures as appropriate.
The Group realizes that one of the sustainability risks associated with its business activities is the possible negative impacts of pharmaceutical manufacturing and its by-products on the environment. There have been incidents in the past in which by-products of pharmaceutical manufacturing were detected in rivers and other natural environments. The Group aware that social concern is rising with regard to this issue as well as its potential environmental repercussions. The Group watches closely such social responses and the global trend toward promotion of initiatives for EPS*2 by the European Federation of Pharmaceutical Industries and Associations (EFPIA).
We believe that we need to continuously coordinate with governments, industry organizations, and research institutions to examine more appropriate risk evaluations and risk management.
*2EPS(Eco-Pharmaco-Stewardship): Voluntary initiatives to prevent environmental impacts throughout the lifecycle of pharmaceuticals and eco-friendly product management.
Environmental Impact Assessment of the Manufacturing Processes
As the changes in manufacturing processes for pharmaceutical products are regulated by pharmaceutical related laws and regulations, such changes require considerable time and effort. Accordingly, it is important to discuss and evaluate changes not only from the view of quality and cost, but also from a wide range of perspectives including impact on the environment.
When developing manufacturing processes for new products, the Daiichi Sankyo Group uses LIME (Life-cycle Impact assessment Method based on Endpoint modeling), a type of LCA (Life Cycle Assessment) to quantitatively evaluate in each development stage (i.e., start of research, clinical, and commercial stages of manufacturing process development). We integrate toxic and hazardous substances used in manufacturing, energy consumption during manufacturing, and waste discharged during manufacturing into a single assessment target.
This LCA assessment is conducted on new products. The coverage rate of products that have been fully or partially assessed since 2020 is approximately 2/3 of all new products. This approach is based on the concept of eco-friendly green chemistry. Through this approach, we aim to create manufacturing processes that are considerate of the sustainability of the natural environment by developing new synthetic processes, preventing pollution, and reducing resource and energy consumption.
For manufacturing processes that produce waste, we discuss and evaluate methods through which the waste can be collected and reused as well as methods of treating this waste that are highly safe and have a low environmental impact.
The result of this research leads to a great reduction of the environmental impact of the final manufacturing process (industrialized manufacturing method) compared with the impact when this research had just begun.
Implementation of WET testing
With the purpose of assessing the impact of water discharged from operation sites, in FY2021, we continued to conduct WET testing* at all plants and research facilities in Japan (seven operation sites). As a result, we confirmed that the discharged water has no serious impact on aquatic organisms in rivers, etc. In FY2023, we plan to conduct WET testing once at our plants and research facilities in Japan as we do every year to promote appropriate wastewater management and improve the quality of discharged water.
*Whole Effluent Toxicity Test. A testing method that utilizes the biological responses of fish, daphnia, and seaweed to determine the total toxicity of discharged water.
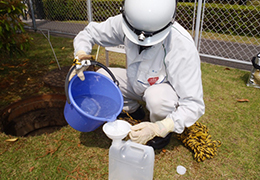
Extracting water for the WET test